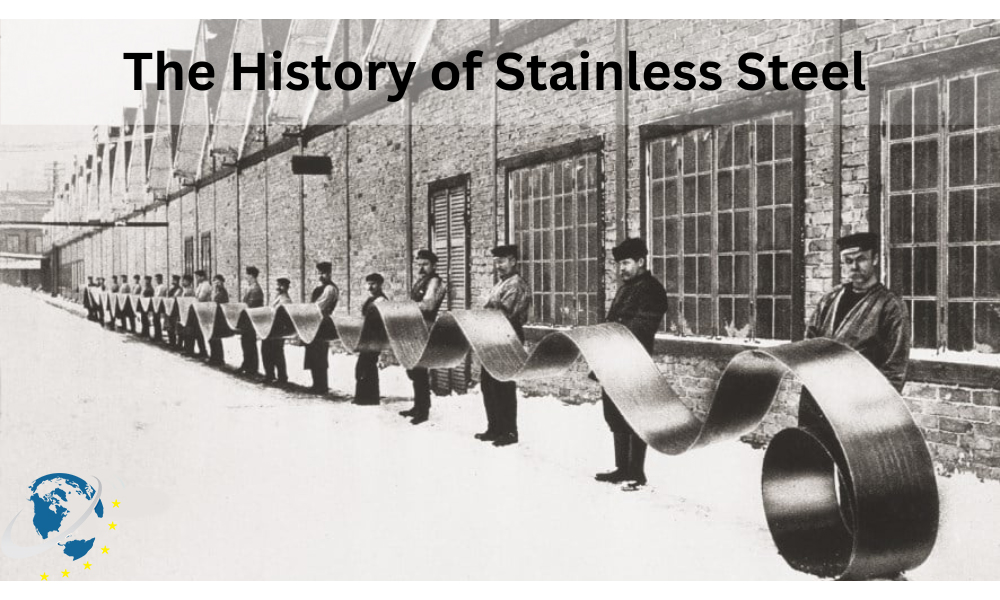
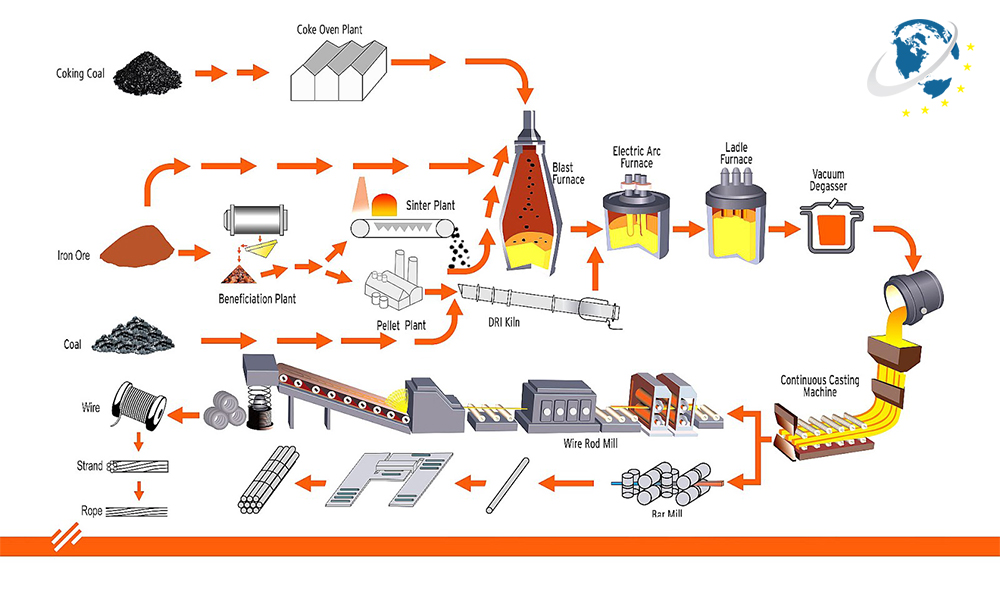
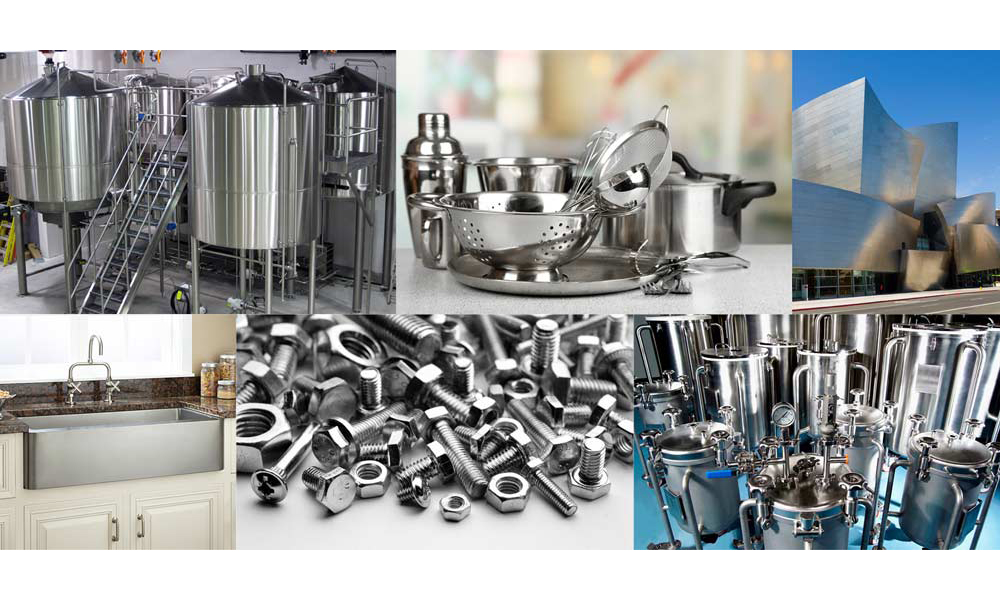
Stainless Steel SuperMarket
- Coil-Sheet: 300-400 Series
- Tube-Profile:300-400 Series
- Long Part: 300-400 Series
- Inquiry: info@minervasteel.com
1-History of Stainless Steel
The invention of stainless steel followed a series of scientific developments, starting in 1798 when chromium was first shown to the French Academy by Louis Vauquelin. In the early 1800s, British scientists James Stoddart, Michael Faraday, and Robert Mallet observed the resistance of chromium-iron alloys ("chromium steels") to oxidizing agents. Robert Bunsen discovered chromium's resistance to strong acids. The corrosion resistance of iron-chromium alloys may have been first recognized in 1821 by Pierre Berthier, who noted their resistance against attack by some acids and suggested their use in cutlery. In the 1840s, both of Britain's Sheffield steelmakers and then Krupp of Germany were producing chromium steel with the latter employing it for cannons in the 1850s. In 1861, Robert Forester Mushet took out a patent on chromium steel in Britain. These events led to the first American production of chromium-containing steel by J. Baur of the Chrome Steel Works of Brooklyn for the construction of bridges. A US patent for the product was issued in 1869. This was followed with recognition of the corrosion resistance of chromium alloys by Englishmen John T. Woods and John Clark, who noted ranges of chromium from 5–30%, with added tungsten and "medium carbon". They pursued the commercial value of the innovation via a British patent for "Weather-Resistant Alloys"
2-Properties
a-Conductivity
Like steel, stainless steels are relatively poor conductors of electricity, with significantly lower electrical conductivities than copper. In particular, the electrical contact resistance (ECR) of stainless steel arises as a result of the dense protective oxide layer and limits its functionality in applications as electrical connectors. Copper alloys and nickel-coated connectors tend to exhibit lower ECR values, and are preferred materials for such applications. Nevertheless, stainless steel connectors are employed in situations where ECR poses a lower design criteria and corrosion resistance is required, for example in high temperatures and oxidizing environments.
b-Melting point
As with all other alloys, the melting point of stainless steel is expressed in the form of a range of temperatures, and not a singular temperature. This temperature range goes from 1,400 to 1,530 °C (2,550 to 2,790 °F) depending on the specific consistency of the alloy in question.
c-Magnetism
Martensitic, duplex and ferritic stainless steels are magnetic, while austenitic stainless steel is usually non-magnetic. Ferritic steel owes its magnetism to its body-centered cubic crystal structure, in which iron atoms are arranged in cubes (with one iron atom at each corner) and an additional iron atom in the center. This central iron atom is responsible for ferritic steel's magnetic properties. This arrangement also limits the amount of carbon the steel can absorb to around 0.025%. Grades with low coercive field have been developed for electro-valves used in household appliances and for injection systems in internal combustion engines. Some applications require non-magnetic materials, such as magnetic resonance imaging . Austenitic stainless steels, which are usually non-magnetic, can be made slightly magnetic through work hardening. Sometimes, if austenitic steel is bent or cut, magnetism occurs along the edge of the stainless steel because the crystal structure rearranges itself
d-Corrosion
The addition of nitrogen also improves resistance to pitting corrosion and increases mechanical strength. Thus, there are numerous grades of stainless steel with varying chromium and molybdenum contents to suit the environment the alloy must endure. Corrosion resistance can be increased further by the following means: • increasing chromium content to more than 11% • adding nickel to at least 8% • adding molybdenum (which also improves resistance to pitting corrosion)
e-Wear
Galling, sometimes called cold welding, is a form of severe adhesive wear, which can occur when two metal surfaces are in relative motion to each other and under heavy pressure. Austenitic stainless steel fasteners are particularly susceptible to thread galling, though other alloys that self-generate a protective oxide surface film, such as aluminium and titanium, are also susceptible. Under high contact-force sliding, this oxide can be deformed, broken, and removed from parts of the component, exposing the bare reactive metal. When the two surfaces are of the same material, these exposed surfaces can easily fuse. Separation of the two surfaces can result in surface tearing and even complete seizure of metal components or fasteners. Galling can be mitigated by the use of dissimilar materials (bronze against stainless steel) or using different stainless steels (martensitic against austenitic). Additionally, threaded joints may be lubricated to provide a film between the two parts and prevent galling. Nitronic 60, made by selective alloying with manganese, silicon, and nitrogen, has demonstrated a reduced tendency to gall.
Types
a-Austenitic
Austenitic stainless steel is the largest family of stainless steels, making up about two-thirds of all stainless steel production. They possess an austenitic microstructure, which is a face-centered cubic crystal structure.]This microstructure is achieved by alloying steel with sufficient nickel and/or manganese and nitrogen to maintain an austenitic microstructure at all temperatures, ranging from the cryogenic region to the melting point. Thus, austenitic stainless steels are not hardenable by heat treatment since they possess the same microstructure at all temperatures. Austenitic stainless steels sub-groups, 200 series and 300 series: • 200 series are chromium-manganese-nickel alloys that maximize the use of manganese and nitrogen to minimize the use of nickel. Due to their nitrogen addition, they possess approximately 50% higher yield strength than 300 series stainless sheets of steel. o Type 201 is hardenable through cold working. o Type 202 is a general-purpose stainless steel. Decreasing nickel content and increasing manganese results in weak corrosion resistance. • 300 series are chromium-nickel alloys that achieve their austenitic microstructure almost exclusively by nickel alloying; some very highly alloyed grades include some nitrogen to reduce nickel requirements. 300 series is the largest group and the most widely used. o Type 304: The best-known grade is Type 304, also known as 18/8 and 18/10 for its composition of 18% chromium and 8% or 10% nickel, respectively. o Type 316: The second most common austenitic stainless steel is Type 316. The addition of 2% molybdenum provides greater resistance to acids and localized corrosion caused by chloride ions. Low-carbon versions, such as 316L or 304L, have carbon contents below 0.03% and are used to avoid corrosion problems caused by welding.
b-Ferritic
Ferritic stainless steels possess a ferrite microstructure like carbon steel, which is a body-centered cubic crystal structure, and contain between 10.5% and 27% chromium with very little or no nickel. This microstructure is present at all temperatures due to the chromium addition, so they are not hardenable by heat treatment. They cannot be strengthened by cold work to the same degree as austenitic stainless steels. They are magnetic. Additions of niobium (Nb), titanium (Ti), and zirconium (Zr) to Type 430 allow good weldability. Due to the near-absence of nickel, they are less expensive than austenitic steels and are present in many products, which include: • Automobile exhaust pipes (Type 409 and 409 are used in North America; stabilized grades Type 439 and 441 are used in Europe) • Architectural and structural applications (Type 430, which contains 17% Cr) • Building components, such as slate hooks, roofing, and chimney ducts • Power plates in solid oxide fuel cells operating at temperatures around 700 °C (1,300 °F) (high-chromium ferritics containing 22% Cr)
c-Martensitic
Martensitic stainless steels have a body-centered cubic crystal structure, and offer a wide range of properties and are used as stainless engineering steels, stainless tool steels, and creep-resistant steels. They are magnetic, and not as corrosion-resistant as ferritic and austenitic stainless steels due to their low chromium content. They fall into four categories (with some overlap) • Fe-Cr-C grades. These were the first grades used and are still widely used in engineering and wear-resistant applications. • Fe-Cr-Ni-C grades. Some carbon is replaced by nickel. They offer higher toughness and higher corrosion resistance. Grade EN 1.4303 (Casting grade CA6NM) with 13% Cr and 4% Ni is used for most Pelton, Kaplan, and Francis turbines in hydroelectric power plants because it has good casting properties, good weldability and good resistance to cavitation erosion. • Precipitation hardening grades. Grade EN 1.4542 (also known as 17-4 PH), the best-known grade, combines martensitic hardening and precipitation hardening. It achieves high strength and good toughness and is used in aerospace among other applications. • Creep-resisting grades. Small additions of niobium, vanadium, boron, and cobalt increase the strength and creep resistance up to about 650 °C (1,200 °F). Martensitic stainless steels can be heat treated to provide better mechanical properties. The heat treatment typically involves three steps: 1. Austenitizing, in which the steel is heated to a temperature in the range 980–1,050 °C (1,800–1,920 °F), depending on grade. The resulting austenite has a face-centered cubic crystal structure. 2. Quenching. The austenite is transformed into martensite, a hard body-centered tetragonal crystal structure. The quenched martensite is very hard and too brittle for most applications. Some residual austenite may remain. 3. Tempering. Martensite is heated to around 500 °C (930 °F), held at temperature, then air-cooled. Higher tempering temperatures decrease yield strength and ultimate tensile strength but increase the elongation and impact resistance. Replacing some carbon in martensitic stainless steels by nitrogen is a recent development.[ The limited solubility of nitrogen is increased by the pressure electroslag refining (PESR) process, in which melting is carried out under high nitrogen pressure. Steel containing up to 0.4% nitrogen has been achieved, leading to higher hardness and strength and higher corrosion resistance. As PESR is expensive, lower but significant nitrogen contents have been achieved using the standard AOD process.
d-Duplex
Duplex stainless steels have a mixed microstructure of austenite and ferrite, the ideal ratio being a 50:50 mix, though commercial alloys may have ratios of 40:60. They are characterized by higher chromium (19–32%) and molybdenum (up to 5%) and lower nickel contents than austenitic stainless steels. Duplex stainless steels have roughly twice the yield strength of austenitic stainless steel. Their mixed microstructure provides improved resistance to chloride stress corrosion cracking in comparison to austenitic stainless steel Types 304 and 316. Duplex grades are usually divided into three sub-groups based on their corrosion resistance: lean duplex, standard duplex, and super duplex. The properties of duplex stainless steels are achieved with an overall lower alloy content than similar-performing super-austenitic grades, making their use cost-effective for many applications. The pulp and paper industry was one of the first to extensively use duplex stainless steel. Today, the oil and gas industry is the largest user and has pushed for more corrosion resistant grades, leading to the development of super duplex and hyper duplex grades. More recently, the less expensive (and slightly less corrosion-resistant) lean duplex has been developed, chiefly for structural applications in building and construction (concrete reinforcing bars, plates for bridges, coastal works) and in the water industry.
4-Grade 200-300-400 series
Grades Which are Most Used in Our Country 304 – 304L: It is the most known grade of the austenitic group. It provides high oxidation up to 400 °C. Its mechanical resistance and friction resistance are particularly good. Its form with low carbon content is referred to as 304L. It is used in the production of kitchenware, sinks, household appliances, industrial kitchens, chemical and petrochemical industry, food industry, automotive industry, heat exchanger and boiler. 316 – 316L – 316 Ti: It is resistant to temperatures up to 600 °C. Its mechanical rupture and shrinkage resistance are particularly good. Due to its molybdenum content, it is resistant to oxidation and acids. Its low-carbon state, which is resistant to temperatures up to 400 °C, is 316 and its variety with titanium resistance to high temperature and oxidation is 316Ti. It is used in the chemistry, petrochemical industry, steam boilers, heat-resistant exchangers, various boiler applications. 316L group is used in dairy and nuclear engineering and paper industry. 316Ti group is used in pump and compressor parts, boilers, furnaces, and heat exchangers. 321: Its corrosion resistance has been enhanced by the addition of Titan. It is resistant to high temperatures. It is used in heat exchangers, resistances, exhaust pipes, aviation industry, breweries, chemical industry. 309S: Its oxidation resistance is high at temperatures up to 1050 °C. It is used in the production of equipment and parts resistant to high temperatures. 310-310S: Its oxidation resistance is high at temperatures up to 1100 °C. It is used in furnace parts and equipment resistant to high temperatures, chemical, petrochemical industry. 430: It is the most used grade of the ferritic group. It provides a good surface appearance. It can be magnetized since it does not contain nickel. Decorative uses, glossy surface applications. 441: It provides high-temperature resistance and good corrosion resistance. It can be used in Exhaust systems, Elevator, and Heat exchanger manufacturing. 200: Group 201 which is most widely used, contains the lowest nickel. It is classified as J1-J2-J4-J6 within itself. It yields better results in drawing processes due to the copper content of 204CU. It is used in decorative uses, industrial kitchen, elevator, warehouse manufacturing.
5-Stainless Steel Application
• Automotive and transportation Stainless steel was introduced in automotive in the 1930s by Ford to manufacture their concept cars. Since then, it is used to produce a variety of automotive parts such as exhaust systems, grills, and trims. With advancing technology, stainless steel is being favoured by manufacturers to make structural components. It is also heavily featured in other fields of transportation like freighting to make shipping containers, road tankers and refuse vehicles. It’s resistance to corrosion makes it ideal to transport chemicals, liquids and food products. The low maintenance of stainless steel also makes it an easy and cost-effective metal to clean and sustain. • Medical technology Stainless steel is preferred in clean and sterile environments as it is simple to clean and does not easily corrode. Stainless is used in the production of a wide range of medical equipment, including surgical and dental instruments. It is also used in building operation tables, kidney dishes, MRI scanners, cannulas, and steam sterilizers. Most surgical implants, such as replacement joints and artificial hips are made from stainless steel, as well as some joining equipment like stainless steel pins and plates to repair broken bones. • Building trade Due to its strength, resistance, and flexibility, stainless steel application has become a vital element of the building trade. It is commonly featured in the interior on countertops, backsplashes, and handrails, and is also used externally in cladding for high impact buildings. It is a common feature in modern architecture due to its weldability, easy maintenance and attractive finish, which is used in the Eurostar Terminal in London and the Helix Bridge in Singapore. With the movement towards sustainable building, stainless steel, which is a highly recyclable metal, is becoming increasingly preferable to use in construction. With a polished or grain finish, it has aesthetically pleasing properties and can aid in improving natural lighting in the building. • Aircraft construction The aviation industry also has a preference for stainless steel. It is used in various applications including the frames of aeroplanes because of its strength and ability to withstand extreme temperatures. It can also be applied in jet engines as it can help prevent against its rusting. Why not also read aircraft grade aluminum. Stainless steel is also an essential part of the landing gear. Its strength and rigidity can handle the weight of the landing aircraft. • Food and the catering industry In the food and catering industry, stainless steel is used to manufacture kitchen accessories, cookware, and cutlery. Utensils such as knives are made using less ductile grades of stainless steel. The more ductile grades are used to make grills, cookers, saucepans, and sinks. Stainless steel can also be used to finish freezers, dishwashers, refrigerators, and countertops. In food production, stainless steel is ideal because it doesn’t affect the flavour of the food. It is also corrosion resistant, and hence able to hold acidic drinks including orange juice. The ease of cleaning stainless steel makes it difficult to harbour bacteria, adding to its usefulness in food storage. • Tanker manufacture • Vessel manufacture